With any project or experiment that you undertake, the data that it produces will ultimately determine the fruits of your labor. Without data, we wouldn’t be able to understand how a system actually performs.
For example, if you want to set up a heating coil that can help the object to reach a specific temperature, you cannot understand its level of success without measuring the temperature. A simple task as measuring and recording the temperature is as Data Acquisition. Another example is measuring and recording the current difference across a resistor.
In essence, data acquisition is a process that involves collecting information to understand the electrical or physical phenomenon using sensors, measurement device, and a computer. Together, these components form a Data Acquisition System or DAQ System.
In this guide, you’ll learn about:
- What is a DAQ system?
- Basic components of a DAQ system
- How to measure with a DAQ device?
- Factors affecting the measurement accuracy
- Benefits of using DAQ devices
- Important applications of the DAQ system
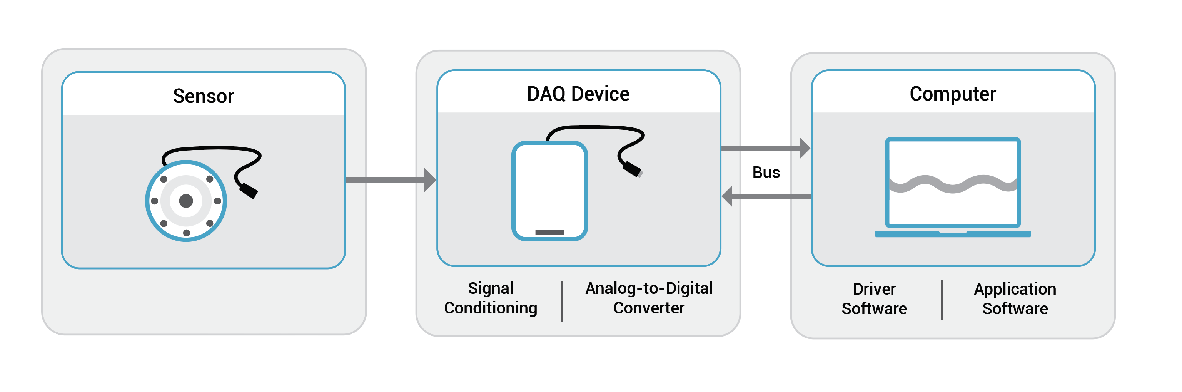
What is a DAQ System?
As discussed already, DAQ or Data Acquisition comprises a measurement system and a computer that can measure electrical or physical properties and record them for further analysis.
The concept of DAQ was introduced in 1963 where it mainly revolved around monitoring or controlling a physical entity with software. IBM was the first to announce a computer that was solely made for data acquisition tasks called the IBM 7700 Data Acquisition system.
The IBM 7700 was replaced with a more powerful IBM 1800 Data Acquisition and Control System in 1964. With the progress in technology, the computing capabilities have drastically changed today, allowing us to quickly process and store data in numerous ways.
DAQ systems are an excellent example of this. These devices are capable of capturing data from an actual system and store that data in an easily retrievable format for further engineering or scientific review.
Considering the intuitiveness of the DAQ systems, these computer-based measurement systems are of critical importance in a variety of verticals that need precision, such as construction, electronics, production, and manufacturing to name a few.
DAQ systems are either handheld or can be operated remotely. Handheld DAQ systems are useful when you are required to take readings of a specimen with which you can physically interact. Remote DAQ measurements are taken where human presence is incompatible.
Basic Components of a DAQ SystemThe IBM machines of 1960 where gigantic 6-foot-high computers. Thankfully, the modern DAQ systems are compact, yet many times more powerful than their predecessors.
Years of technological advancements in electronics have made it possible to have such sleek machines that do not compromise on measurement accuracy.
A basic DAQ system consists of four parts:
Sensors
Sensors or transducers interact with the subject measured, either directly or indirectly (contact or non-contact). They covert the physical values to electric signals. The type of sensors used in a DAQ system varies based on the nature of its application.
For example, the measurement of temperature requires a temperature sensor, while a photovoltaic sensor is useful for measuring light. Their common function is to covert analogic signals like light, temperatures, speed, etc. into digital signals for the computer. DAQ systems employ high-quality sensors that give accurate readings with minimal or no noise.
Transmission/Signal Conditioning
The electrical signals impending from the sensors cannot be utilized directly, as it needs modification. This modification is necessary because the signals often contain noise or might be weak to a point where the DAQ system cannot measure it.
Hence an additional circuitry is used to optimize the signals, termed as a signal conditioner. The process of optimizing the signals is known as signal conditioning.
The signal conditioner uses filter circuits to separate the noise from the real signal and uses an amplification circuit to strengthen weak signals. These are two of the common functions that they undertake.
There are even more processes like calibration, linearization, and excitation that achievable with a suitable signal conditioning circuit. The selection of the signal conditioning circuit largely depends on the characteristics of the sensor.
DAQ Hardware
DAQ hardware is the hardware entity connected between the computer and the sensors. DAQ hardware is either connected to the computer using the USB ports or through the PCI-Express slots on the motherboard.
The DAQ hardware takes in the analog signals from the sensors and converts them to digital signals readable by the computers. But, this is just one of the functions of DAQ hardware.
Some of the common features in a DAQ system are:
ADC: Converts analog signals into digital signals
Digital to analog converter: Support for inputting and outputting binary signals
RS232, RS485: Interface busses used to communicate with other devices
Single-ended input: Support for taking input from single-ended wires
There is even a standalone DAQ hardware that can operate on its own without requiring a connection to a computer. This is possible through a processor and computing unit embedded within the DAQ hardware. Standalone DAQ hardware is capable of helping users with real-time data representation.
Standalone oscilloscopes and data loggers are prime examples of DAQ systems that can work without a computer.
Computer
The end piece of the DAQ chain is a computer that gathers all the data coming through the DAQ hardware for further analysis. However, connecting the DAQ hardware to a computer is not enough to make sense of the data.
It requires a DAQ software that uses the data from the DAQ hardware to create readable and meaningful results. In other words, the DAQ software acts as the layer between the user and the DAQ hardware. Computers are critical to performing higher-order computations with the data collected from the DAQ.