With the objective of developing a better, more efficient, and more cost-effective alternative to the status quo method for accurately measuring the temperature of fluid media inside of a pipe – which is to use an invasive immersion probe – a team of Omega engineers, led by Director of Engineering Ken Leibig, developed the groundbreaking HANI High Accuracy, Non-Invasive Clamp Temperature Sensor.
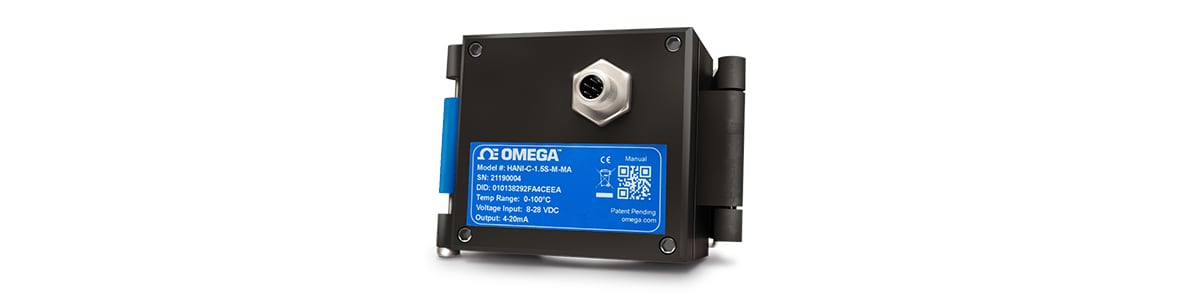
Featuring technology based on Fourier’s law of heat conduction, the HANI does what few thought was even possible: it installs with the ease of a surface sensor yet offers the high accuracy and high performance of an immersion sensor.
The HANI is a complete game-changer for professionals in a wide array of industries – from Food & Bev to Pharmaceutical to Aerospace – as it provides a versatility unattainable with immersion sensors without sacrificing any accuracy.
With such versatility, the HANI is an ideal solution for many common industrial temperature measurement challenges.
The HANI is the Shortcut that ACTUALLY Works
Getting around immersion sensor installation is something that many systems managers, systems operators, are looking to do. And who’d blame them? Installing immersion sensors is an expensive and time-consuming process that, despite temperature measurement being essential in so many industrial applications and manufacturing processes, is sometimes not even a viable option.
Systems operators and managers will often turn to non-contact devices like infrared (IR) thermometers for a quick-and-easy solution. Yet these shortcuts never work.
Until now. The HANI is the shortcut that ACTUALLY works.
Don’t want to deal with sensor probe installation? Can’t deal with it? No problem.
HANI installation is a breeze because, well, there is none. Clamp a HANI sensor to any desired location along a pipe and you’ve got an accurate temperature measurement of the fluid media inside – instantly.
The HANI Can Verify the Accuracy of an Existing Immersion Sensor
One of the annoying aspects of immersion sensors is that, because they’re installed into the system itself, accessing them is a royal pain in the neck – and requires shutting down the process, which, of course, means costly downtime. Ideally, you’d just never even touch them. But if one of your immersion sensors starts showing a regular increase in temperature, the sensor is going to have to be un-installed, inspected, and, potentially, calibrated.
That’s where the HANI comes in. Remember, the HANI mounts in seconds – it clamps right onto the outside of a pipe – and can be placed practically anywhere you want. So, to verify an immersion sensor that is showing a concerning increase in temperature, just mount a HANI sensor next to it. If both sensors are reading the same temperature, well, you better stop the process and investigate. But if the HANI sensor indicates there is no change in temperature, you can continue monitoring while running your process uninterrupted – preventing unnecessary and costly downtime.
Relocating an Already-Installed Immersion Sensor? Are you Crazy? Just use a HANI
The installation of a traditional immersion sensor is not a simple process. Installation requires shutting down the system, which means costly downtime, and invasive cutting and welding on the pipe itself. Once an immersion sensor is installed, relocation is not a viable option. If the location of an immersion sensor needs to be changed, the sensor needs to be uninstalled and then re-installed in the desired location – requiring more downtime and more invasive construction.
Since installation is a breeze, just leave your existing invasive sensor where it is and use a HANI.
A HANI can basically install anywhere – all you have to do is clamp it to the outside of the desired pipe – and, if relocation is needed again, simply remove the HANI and clamp it wherever it is needed next.
HANI: Faster than a Speeding Bullet
The HANI was designed to address the challenge of measuring in-pipe media temperature. The challenge with obtaining this data is that to accurately measure the temperature of the media, sensors need direct contact – meaning the installation of invasive sensor probes. Widely used sensors like thermocouples and RTDs not only provide the accuracy that industrial and manufacturing professionals need, but they also provide the speed needed.
When the installation of invasive immersion sensors is not possible, professionals often turn to inferior temperature sensors, like surface sensors. However, these types of sensors do not provide the speed that is often needed in industrial processing and manufacturing.
The HANI, which installs like a surface sensor, is able to provide not only the high level of accuracy that is expected of industrial temperature sensors, but also the high-level of speed. HANI sensors provide data that can be viewed immediately.
No More Inclusion Woes
One of the issues with using traditional immersion sensors is that the consistency of the media that is being processed needs to be taken into consideration. For example, if the media being processed has inclusions, this will cause an issue for immersion sensors.
An immersion sensor requires that a sensor probe be installed inside of the pipe, so that it can come in direct contact with the process media. If the media has inclusions, those inclusion can, over time, build up around the sensor probe.
This becomes an issue because this buildup can cause sensor drift and affect the accuracy of the sensor.
HANI sensors, which are non-invasive and require zero contact with the media of which the temperature it is measuring (hence the NI in the name HANI), simply do not have this problem.
Not Just Clean – HANI Clean
Regular cleaning of a system is common practice in many industries, and quite often an effective cleaning system is necessary for the quality of a product to remain consistent. While in the past cleaning was done manually, it has become standard practice in many industries to use automated Clean in Place (CIP) systems to clean and maintain processing systems and equipment.
HANI sensors are ideal for CIP systems because this cleaning process requires accurate temperature monitoring. During various stages of a CIP process, CIP cleaning agents need to be heated to the correct temperature range so that they can thoroughly clean the interior or processing equipment.
Traditional immersion sensors are so difficult and costly, that systems operators would simply not use temperature sensors during this critical process.
However, the ease and versatility of a HANI sensor – not to mention its high accuracy (equal to that of immersion sensors) – means that systems operators no longer have to guess at temperatures during the CIP process. Instead, CIP systems can run with the confidence that accurate temperature monitoring provides.
The HANI Let’s the ‘Pig’ Fly
In order to increase product yields and to reduce costs in a variety of manufacturing industries, product recovery systems (or ‘pigging’ systems) are used to recover any residual product left in the piping system. A pigging system consists of the ‘pig’, which is a solid projectile or plug, that has a diameter slightly larger than the pipeline or tubing that is transporting the media. The ‘pig’ is introduced into the pipeline and is pushed through the pipe – forcing all residual product along with it.
However, while a pigging system is effective in reducing the amount of time, water, chemicals, labor, and energy needed to run a CIP system, you can’t run a pig through a system if there are sensor probes installed. These sensor probes – as well as the protective thermowells installed to house them – impede the pig, making the process impossible without removing them first. And costly added downtime is the inevitable result.
Since HANI sensors are completely non-invasive, the product recovery system can run without the need to remove and replace sensors. This not only prevents contamination risks, but also reduces labor time and increases productivity.