Volumetric flow meters are types of flow meters that operate linearly with respect to the volume flow rate – they make a flow measurement of the amount of either a liquid or a gas flowing through a pipe by measuring the velocity at which it is flowing. Volumetric flow meters measure volumetric flow rate, differing from mass flow meters, like Coriolis flow meters, which calculate mass flow rate by measuring the amount of mass passing through a pipe or device for a given amount of time. Because there is no square-root relationship (as with differential pressure devices), their rangeability is greater. Volumetric flow meters have minimum sensitivity to viscosity changes when used at Reynolds numbers above 10,000. Most velocity-type meter housings are equipped with flanges or fittings to permit them to be connected directly into pipelines.
View Omega's entire portfolio of flow meters.
What are the Types of Volumetric Flow Meters
There are several different volumetric flow meter types, and they are popular because they provide a direct measure of flow velocity.
Volumetric flow meter types include:
Positive Displacement Flow Meters
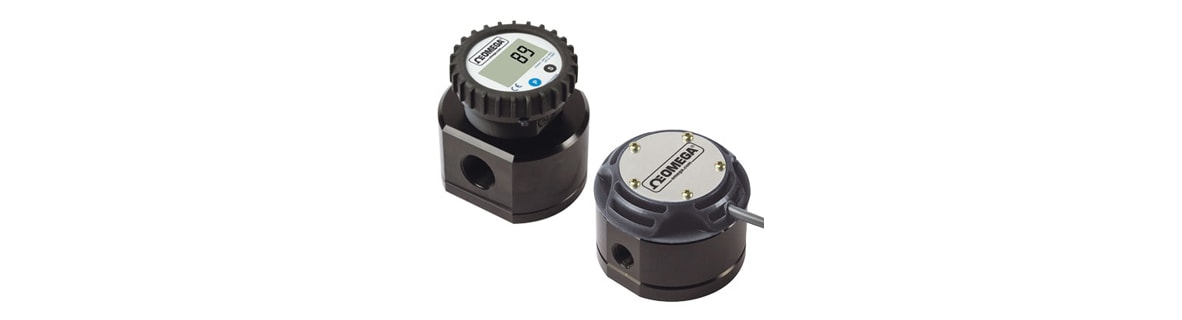
Positive displacement flow meters measure flow rate by dividing flowing media into fixed, metered volumes and timing the rate at which these set levels are reached. By counting the number of passed isolated volumes, a flow measurement is obtained. Positive displacement flow meters provide high accuracy at low flow.
Turbine Flow Meters
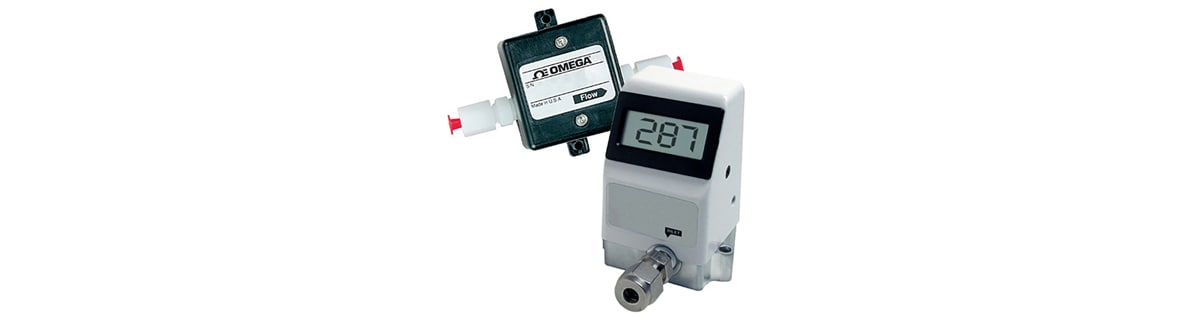
Turbine meters are widely used for accurate liquid measurement applications. These units consist of a multiple-bladed rotor mounted within a pipe, perpendicular to the fluid flow. The rotor spins as the liquid passes through the blades. The rotational speed is a direct function of flow rate and can be sensed by a magnetic pick-up, photoelectric cell, or gears. Electrical pulses can be counted and totalized.
The number of electrical pulses counted for a given period of time is directionally proportional to flow volume. A tachometer can be added to measure the turbine’s rotational speed and to determine the liquid flow rate. Turbine meters, when properly specified and installed (and with proper calibration), have good accuracy, particularly with low-viscosity liquids.
Electromagnetic Flow Meters
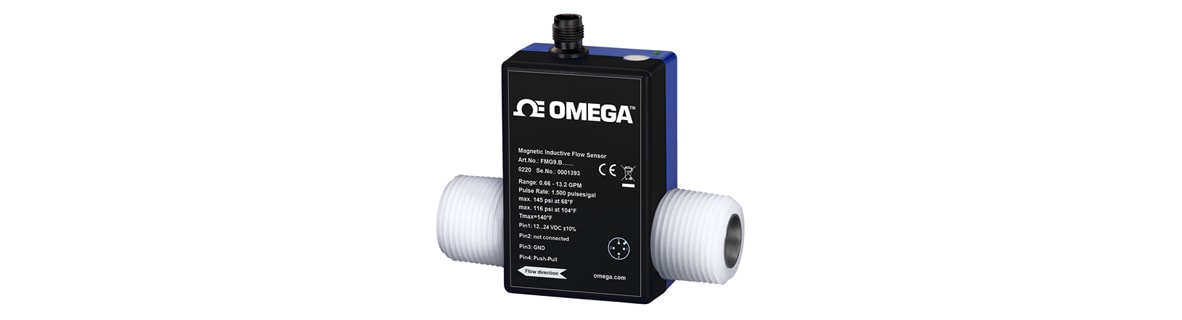
Electromagnetic meters, also known as magnetic flow meters or magmeters, operate pursuant to Faraday’s law of electromagnetic induction – which states that a voltage will be induced when a conductor moves through a magnetic field. Electromagnetic meters can handle most liquids and slurries – provided that the material being metered is electrically conductive. Major components are the flow tube (primary element) and a voltmeter (secondary element). The flow tube mounts directly in the pipe. Pressure drop across the meter is the same as it is through an equivalent length of pipe because there are no moving parts or obstructions to the flow. The voltmeter can be attached directly to the flow tube or can be mounted remotely and connected to it by a shielded cable.
Electromagnetic flow meters have major advantages: They can measure difficult and corrosive liquids and slurries and can measure forward as well as reverse flow with equal accuracy.
Vortex meters
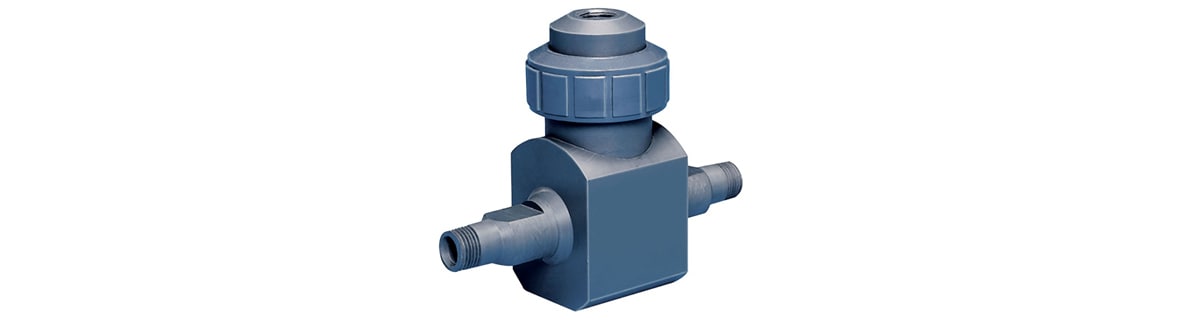
Vortex meters make use of a natural phenomenon that occurs when a liquid flows around a bluff object. Eddies or vortices are shed alternately downstream of the object. The frequency of the vortex shedding is directly proportional to the velocity of the liquid flowing through the meter. Vortex meters measure volumetric flow rate based off a measurement of the frequency of the shedding.
Electromagnetic flow meters have major advantages: They can measure difficult and corrosive liquids and slurries and can measure forward as well as reverse flow with equal accuracy.
Ultrasonic Flow Meters
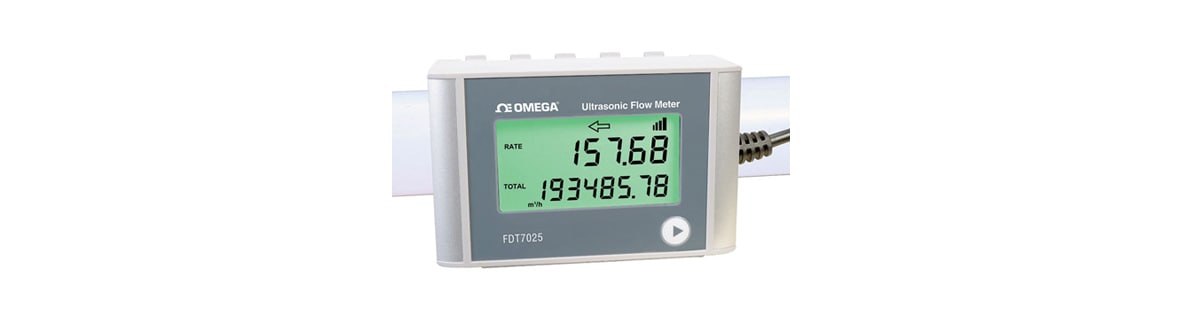
Ultrasonic flow meters can be divided into Doppler meters and time-of-travel (or transit) meters. Doppler meters measure frequency shifts caused by liquid flow. Two transducers are mounted in a case attached to one side of the pipe. A signal of known frequency is sent into the liquid to be measured. Solids, bubbles, and any discontinuity in the liquid cause the pulse to be reflected to the receiver element. Because the liquid causing the reflection is moving, the frequency of the returned pulse is shifted. The frequency shift is proportional to the liquid's velocity.
Time-of-travel meters have transducers mounted on each side of the pipe. The configuration is such that the sound waves traveling between the devices are at a 45-degree angle to the direction of the liquid flow. The speed of the signal traveling between the transducers increases or decreases with the direction of transmission and the velocity of the liquid being measured. A time-differential relationship proportional to the flow can be obtained by transmitting the signal alternately in both directions.